A indústria 4.0 avança em sua marcha e os controladores são importantes para o sucesso
Imagine um sistema de climatização em uma fábrica. Os controladores industriais são responsáveis por receber informações dos sensores de temperatura e umidade, processar esses dados e enviar comandos aos equipamentos, como condicionadores de ar e ventiladores, para manter as condições ambientais dentro de parâmetros predefinidos.
Sem este equipamento, seria necessário monitorar manualmente as condições do ambiente e ajustar os equipamentos de forma constante, o que demandaria tempo, esforço e poderia levar a erros humanos.
A seguir, falamos mais a fundo sobre a importância de empregar o CLP!
O que são controladores?
Os controladores remotos industriais são dispositivos eletrônicos empregados na regulação e supervisão de processos automatizados. Sua finalidade é receber dados provenientes de sensores, processá-los e emitir comandos para atuadores, de modo a garantir que o procedimento permaneça dentro de limites pré-estabelecidos.
Esses aparelhos, a exemplo dos controladores PLUS + 1, podem apresentar uma ampla gama de níveis de sofisticação e funcionalidades, indo desde sistemas simples que controlam apenas um parâmetro, como temperatura ou pressão, até sistemas complexos que monitoram e regulam diversos parâmetros simultaneamente.
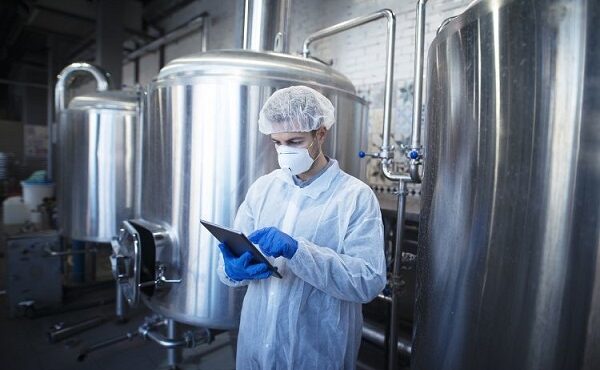
Benefícios do uso de controladores na indústria
A utilização de controlador lógico programável (CLP) traz uma série de vantagens para a automação de processos industriais. Confira alguns exemplos:
Flexibilidade:
Esses dispositivos são altamente flexíveis, permitindo a programação de uma ampla variedade de funções. Isso possibilita aos usuários adaptar o controle de acordo com suas necessidades específicas.
Velocidade e precisão:
Os CLPs são capazes de executar tarefas complexas em alta velocidade, garantindo um controle preciso e confiável do processo industrial.
Confiabilidade:
São bastante confiáveis e possuem recursos para monitorar a operação do processo, identificando eventuais falhas. Caso ocorra algum problema, o sistema é capaz de interromper o processo automaticamente.
Redução de custos:
A utilização do CLP, também conhecidos como PLC (Programmable Logic Controller), resulta em uma redução de custos, uma vez que dispensa o uso de componentes mecânicos, como relés. Além disso, o aumento da eficiência contribui para a economia de recursos.
Maior segurança:
O controlador eletrônico, assim como o rádio controle, pode ser empregado em processos perigosos, garantindo a segurança dos operadores e do processo como um todo.
Monitoramento e diagnóstico:
Os aparelhos têm a capacidade de monitorar e registrar dados do processo, permitindo que os usuários identifiquem e resolvam problemas de maneira mais rápida e eficiente.
Cuidados necessários com os controladores lógico
A seguir, apresentamos algumas precauções a serem observadas com relação aos Controladores Lógicos Programáveis:
- Instalação apropriada: É essencial instalar o dispositivo em um local apropriado, garantindo uma ventilação adequada e proteção contra poeira, umidade e vibrações.
- Fonte de energia estável: O CLP deve ser alimentado por uma fonte de energia estável, compatível com sua potência. Variações na tensão de alimentação podem causar danos ao equipamento.
- Proteção contra sobrecarga: É importante garantir que as cargas conectadas aos controladores estejam dentro dos limites especificados, a fim de evitar sobrecargas que possam danificar o equipamento.
- Limpeza regular: É recomendado realizar limpezas periódicas no controlador remoto industrial para guindaste e outros tipos, removendo poeira e sujeira acumulada. Isso é fundamental para garantir o bom desempenho e funcionamento adequado do dispositivo.