Robôs ABB ajudam fabricante americana de hambúrgueres White Castle a melhorar a produção
A White Castle fabricante líder de hambúrgueres congelados nos EUA utilizou robôs da ABB para agilizar sua produção e evitar lesões aos seus funcionários.
Começando como uma cadeia de fast-food, a White Castle agora tem uma grande operação comercial, vendendo a sua popular linha de mini-hambúrgueres congelados, ou “sliders”, para lojas em todos os EUA.
Uma das principais instalações da empresa é a fábrica de alimentos congelados em Louisville, Kentucky. Ali, a carne de hambúrguer pré-cozida chega em blocos e é fatiada em hambúrgueres individuais. Os bifes de hambúrgueres são colocados manualmente no fundo do pão e depois cobertos com cebola e queijo grelhados e o pão de cima. Os mini-hambúrgueres finalizados são então embalados no fluxo ‘dois por pacote’ e transferidos para um freezer ultra-rápido.
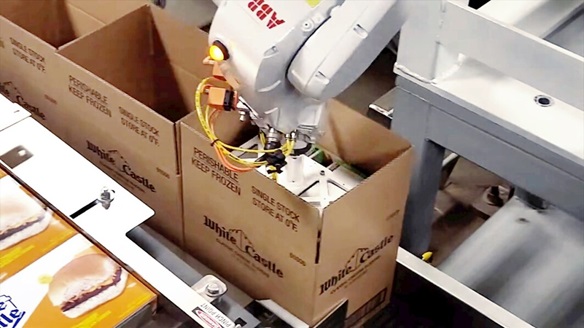
Embalagem e paletização de hambúrgueres congelados da White Castle para envio às lojas.
A partir dali, as embalagens são colocadas em uma esteira que leva a três linhas de embalagem separadas – duas linhas paralelas para caixas de 12 unidades vendidas em lojas em geral e uma linha separada para caixas de 16 unidades vendidas em clubes de atacado.
À medida que a produção de mini-hambúrgueres aumentava, a empresa notou vários gargalos no processo, em especial a embalagem de duas embalagens de mini-hambúrgueres nas caixas para o varejo, uma tarefa altamente repetitiva que envolvia o manuseio de produtos congelados.
Para acelerar esse processo e transferir os funcionários para empregos menos estressantes fisicamente, em 1998 a empresa instalou um IRB 340 FlexPicker® em cada uma das linhas. Equipado com garras de vácuo e motion control sofisticado, cada robô IRB 340 nas linhas de caixas de 12 contagens separa seis embalagens de dois mini-hambúrgueres por vez, enquanto um IRB 360 FlexPicker mais recente na linha de 16 contagens seleciona oito embalagens de duas unidades de cada vez.
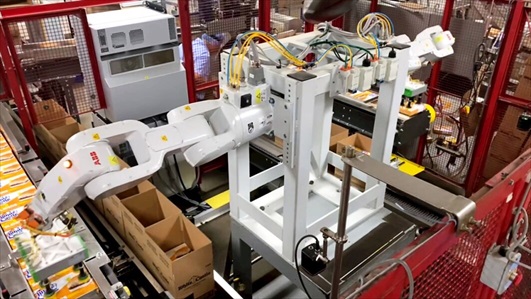
Acelerar o processo de embalagem de hambúrgueres embalados e congelados, evitando possíveis lesões aos funcionários e automatizando o empacotamento e a paletização.
Em cada ciclo, os robôs embalam uma camada de duas caixas simultaneamente, com duas iterações pick-and-place completando duas caixas de cada vez.
Cada um dos modelos originais do IRB 340 ainda está em operação na fábrica de Louisville, mais de vinte anos depois.
“Os robôs delta da ABB são o melhor investimento que já fizemos”, afirma o gerente da fábrica, Tony McGraw. “Sua velocidade e precisão mantêm as linhas em movimento e são altamente confiáveis. Tomamos muito cuidado para mantê-los e continuaremos desta forma. Acho que eles ainda vão durar um bom tempo.”
Confira o vídeo:
Otimizando projetos com o ABB RobotStudio
Depois de um tempo, a White Castle também instalou células robóticas adicionais em duas outras áreas das linhas paralelas – uma para embalar as caixas de varejo em caixas de remessa de 12 unidades e outra para paletizar as caixas de remessa em paletes de 96 caixas. Esses robôs originais serviram esse propósito por muitos anos, mas por fim chegaram à obsolescência.
A White Castle contratou a CIM SYSTEMS INC., uma integradora de sistemas robóticos autorizada pela ABB, para encontrar soluções de substituição para a área de embalagem de papelão e paletização.
Diversos robôs da ABB são usados pela White Castle para realizar o pick de embalagens de produtos congelados, colocá-las em caixas e depois empilhá-las em paletes prontos para envio.
O novo sistema de paletização apresentou alguns desafios no projeto. A primeira era uma área de paletização apertada que precisava acomodar duas linhas inteiras. A solução foi posicionar a extremidade do transportador de cada linha perpendicular à frente do robô, uma logo após a outra, com uma estação de paletes ao longo do lado direito do robô.
A White Castle também queria que o robô retirasse paletes vazios de cerca de 20 quilos de uma pilha e os colocasse na estação de montagem assim que um palete anterior fosse construído e movido para a estação de embalagem extensível. Isso exigiu um design do efetor final mais complexo e movimentos intrincados do robô.
Para desenvolver o design da solução, a CIM utilizou o RobotStudio®, o software de programação offline da ABB, para simular a célula de paletização, incluindo o efetor final especializado, e determinar a posição e o movimento ideais do robô. O uso do software também ajudou a identificar quaisquer gargalos, bem como a calcular requisitos precisos de espaço e tempo de ciclo.
A CIM precisava coordenar o movimento do robô e o padrão do palete, garantindo que a carga passaria pelo primeiro palete, independentemente da sua altura, para chegar com segurança ao segundo palete.
O efetor final era maior que a maioria devido à necessidade de fazer o processo de pick de caixas e paletes. Ele possui ventosas que coletam três caixas de quatro quilos por vez para a operação de paletização, junto com quatro ganchos operados pneumaticamente posicionados em cada canto para manusear com segurança cada palete vazio. Esta combinação permite que o robô execute ambas as funções sem a necessidade de troca de ferramenta.
O RobotStudio ajudou o CIM a projetar e comprovar o desempenho do sistema, acomodando todas as variáveis. O robô paletizador utilizado neste sistema é um IRB 660 ABB de 4 eixos, com alcance de 3,15 metros e carga útil de 180 quilos. Esta configuração proporciona comprimento e resistência suficientes para alcançar e limpar todos os pontos da célula de paletização a partir de uma posição estacionária, tanto horizontal como verticalmente.
Confira o vídeo com várias funcionalidades picking dos robôs ABB
Novos robôs para estação de embalagem de caixas
A mais recente instalação de automação da White Castle apresenta dois robôs ABB IRB 1200 que embalam as caixas de varejo em caixas de expedição de doze contagens – esta estação está localizada após a linha de embalagem e antes dos robôs de paletização. Montados em um pedestal comum entre as duas linhas de embalagem, os dois robôs de menor carga útil usam atuadores de vácuo para selecionar duas caixas que vão para as lojas por vez e colocá-las nas caixas.
Os novos robôs de empacotamento de 5 kg da ABB, um dedicado para cada linha, substituem um único robô maior que atendia ambas as linhas com eficiência cada vez menor à medida que os volumes de produção aumentavam. Os operadores manuais, que anteriormente eram obrigados a auxiliar no processo, foram transferidos para funções mais estratégicas nas instalações.
A CIM usou novamente o RobotStudio para identificar o posicionamento ideal dos robôs com base em sua área ocupada, alcance e carga útil, e para validar o desempenho necessário do sistema em relação aos componentes existentes da linha de embalagem.
“A vasta experiência que tivemos com os robôs FlexPicker da ABB ao longo dos anos fez com que olhássemos atentamente para a ABB quando chegou a hora de substituir nossos outros robôs. Fomos apresentados à CIM SYSTEMS e não poderíamos estar mais felizes”, diz McGraw. “O robô de paletização e os robôs de embalagem realmente aumentaram a eficiência da nossa operação. Eles são sistemas verdadeiramente ‘plug and play’ que exigem suporte manual mínimo.”